El equipo KAIZEN de SEKISUI Alveo de la planta de Bad Sobernheim cosechó un gran éxito con su presentación «Aumento de la proporción de OP en el proceso de laminación». SEKISUI Alveo desarrolla, produce y comercializa espumas de poliolefina de alto rendimiento para revestimientos adhesivos, para la automoción y el sector de la construcción, así como productos industriales y de consumo.
El equipo de SEKISUI Alveo participó en la actividad KAIZEN porque observaron una disminución de la proporción de OP en la laminación como consecuencia del menor tamaño de los lotes y la mayor complejidad de los productos. En consonancia con la política del grupo SEKISUI Alveo, aumentando la proporción de OP, esperaban una reducción de los costes y un aumento de la capacidad. Por medio de un análisis de las 13 labores de modificación de equipos más relevantes y la recopilación de datos en una planta seleccionada, descubrieron que el tiempo de ajuste de los cilindros repartidores correspondientes tenía el mayor impacto en la proporción de OP.
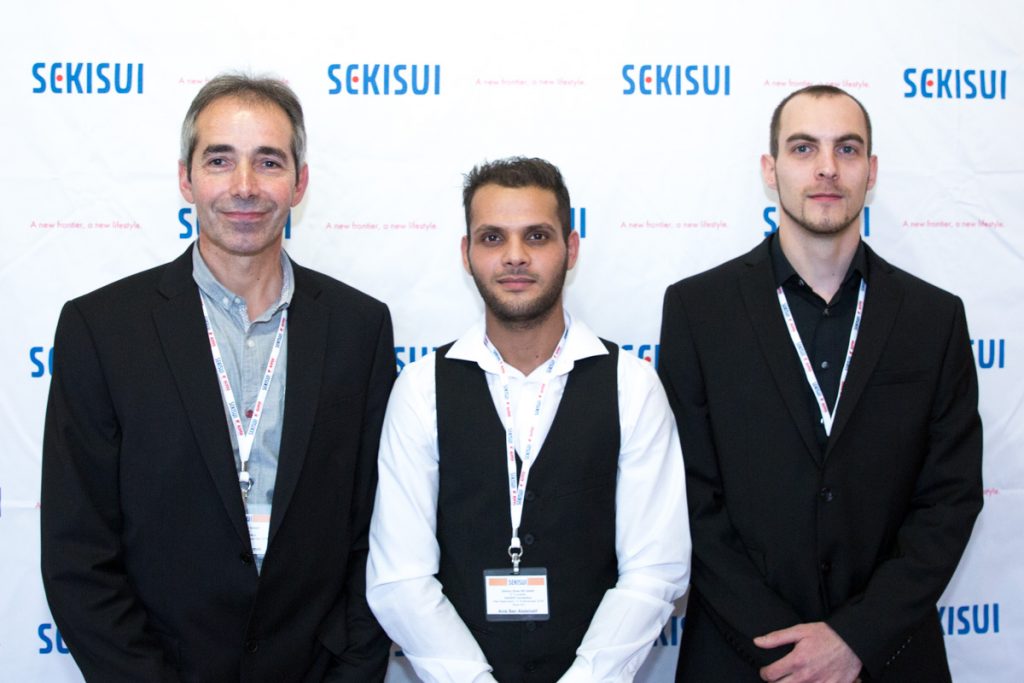
Para examinar los problemas, prepararon un plan de acción y efectuaron un análisis de causas que les llevó a la conclusión de que las causas fundamentales del gasto de tiempo adicional eran las mediciones y el tratamiento manual, así como la necesidad de herramientas especiales. Como consecuencia, el equipo KAIZEN decidió abordar el problema mediante un nuevo diseño de la instalación de cilindros repartidores. Esta medida minimizó el tiempo de instalación, ya que se suprimió la necesidad de reinstalación. Asimismo, se facilitó el ajuste mediante un posicionamiento progresivo y se disminuyó el esfuerzo que debe realizar el operario, así como las probabilidades de error, mediante la colocación de una pantalla y un volante manual.
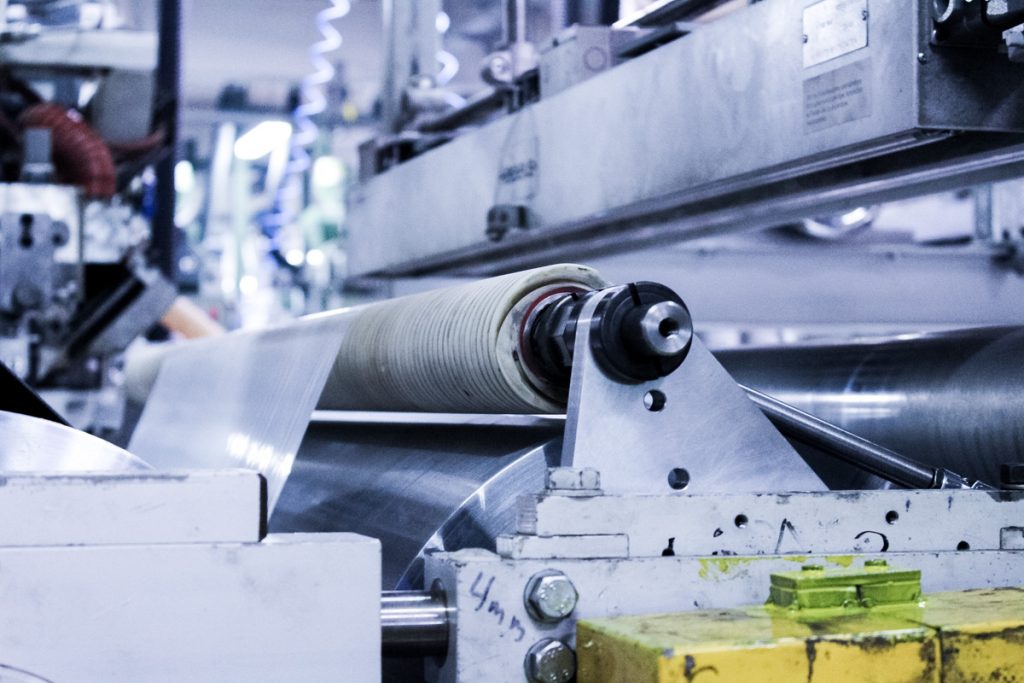
En conjunto, el uso de la nueva instalación de cilindros repartidores en un punto en una planta escogida supuso un ahorro de 30 horas de trabajo y un aumento de la proporción de OP de un 1,8%, lo que dio lugar a unas ventas adicionales estimadas en 60.000 euros. Además, se mejoró la seguridad en el entorno de trabajo. En el futuro, el equipo planea extender el nuevo diseño a todos los cilindros de laminación de su planta y utilizar la recopilación y el análisis de datos para otros proyectos de reducción del tiempo de ajuste. El equipo KAIZEN hizo un excelente trabajo y recibió un merecido reconocimiento.
Aprender más acerca de KAIZEN: KAIZEN 2016: mejora continua por medio del cambio