SEKISUI S-Lec Resin Plant convinced the jury with their presentation “Increase steam condensate”. SEKISUI S-Lec process PVA into PVB powder which is further manufactured into PVB film. This PVB film is used in the automobile industry such as in windshields, sun roofs and side doors. It can also be found in the building construction area to increase safety and additional functionality like sound or solar control to glass windows.
The KAIZEN team found out that there existed a big price gap in production between them and their competitors. In accordance with production policy objectives to reduce fixed cost with a targeted amount of 60.000 Euro per year, they asked themselves, how they can lower the cost of production. Since production has no influence on raw materials and fix costs their solution was to check the utilities of steam, electricity, water and air. The result was that nearly half of the utility costs was based on steam usage caused by greater proportions of steam going to the sewer.
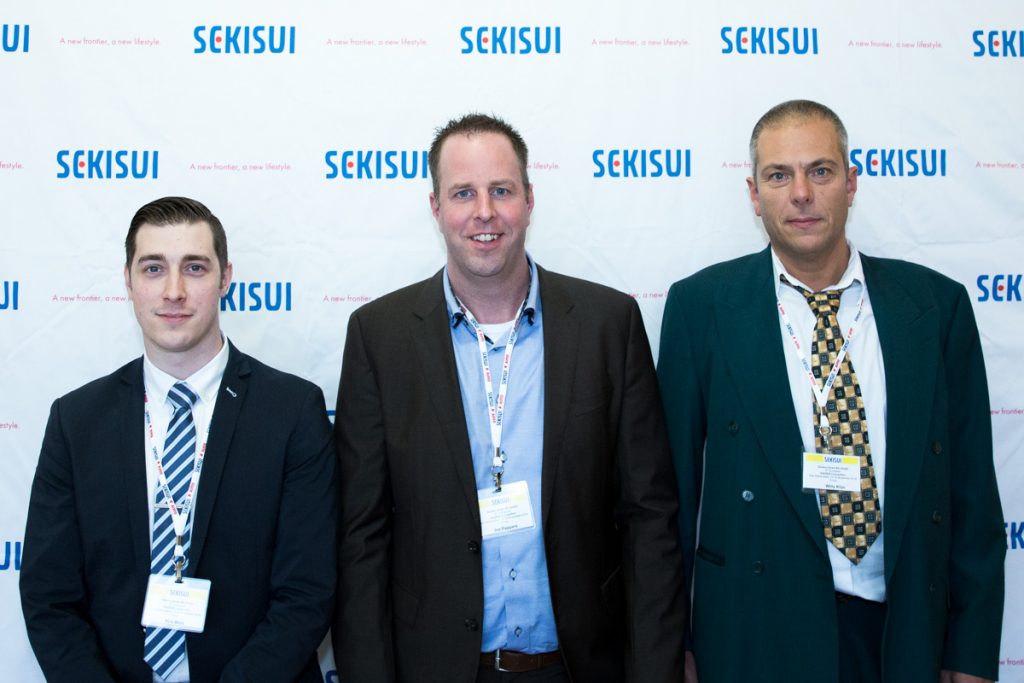
They tackled the problem through the preparation of an action plan, the adjustment of the flowmeter range and the conducting of a cause analysis checking the capacities of the supplier as well as the steam condensate. They also implemented a special hose, which was tested with new settings for one month. The hose was later replaced by a permanent piping. As a result, the KAIZEN team increased the amount of steam condensate going back to the supplier by 1.958 tons per month and therefore reduced the amount of condensate going to the sewer. As a side effect the costs for waste water were also decreased.
Overall, this measures led to a total saving of 5.389 Euro per month or 64.668 Euro per year. Furthermore, the team learned how to cooperate with other companies, when the adjustment of equipment needs certification and management of change. Great project, great work by the SEKISUI S-Lec Resin Plant team.
Learn more about KAIZEN: KAIZEN 2016: Continuous improvement through exchange