In November the seventh KAIZEN Convention takes place. Teams from various European SEKISUI sites, which have previously won internal contests, compete against each other at this event. In the run-up to this year’s convention, we take a look behind the scenes at SEKISUI S-Lec and look at the course of internal KAIZEN activities, from selecting the themes to honouring the winners.
First of all, KAIZEN is a continuous improvement activity in Japanese manufacturing culture. With this activity SEKISUI aims to create a corporate culture of daily improvement of habits in order to raise the ability and growth of each person working on the factory floor or in the office. Thus, SEKISUI contributes to the reinforcement of the company structure and the improvement of business performance.
The highlight of the KAIZEN activity at European level is the annual KAIZEN convention, which takes place this year for the seventh time in Düsseldorf, Germany, on 21 November. Last year, the event was also held in Germany. Back then, SEKISUI Alveo organized the sixth edition of the convention in Geisenheim. In the end, the winner was SEKISUI S-Lec. This year, therefore, we will take a closer look at SEKISUI S-Lec’s internal KAIZEN activities.
The annual SEKISUI S-Lec business plan: the basis of the internal KAIZEN activity
SEKISUI S-Lec operates two plants in the Netherlands – in Roermond and in Geleen – and is specialised in glass interlayer technology for the automotive and the architectural industry. An important aspect of KAIZEN is that the activity is closely linked to company’s policy management. At SEKISUI S-Lec, the Managing Director Yoshio Aoshima draws up a business plan with five to seven major topics each year, which range from profit maximization to workplace safety. The plans of the different departments are based on this business plan. The department’s teams select possible themes on the basis of these topics.
All in all, SEKISUI S-Lec distinguishes between three different types of departments: production, technical and support. The three departments differ in their main areas of activity. While production, for example, is concerned with production-related topics, technical departments focus mainly on topics such as process- and product engineering. Support, on the other hand, covers a wide range of areas such as logistics, finance or Human Resources.
This year a total of 21 teams (10 production, 4 technical and 7 support) took part in the internal KAIZEN competition at SEKISUI S-Lec. And as this year’s technical project “Stable supply PVOH” showed, the competition was not only limited to SEKISUI S-Lec. Cooperation with other European locations were also possible. In this particular project, which dealt with the production of stable Polyvinyl Alcohol (PVOH), researchers from SEKISUI S-Lec and from Sekisui Specialty Chemicals in Tarragona, Spain, were working together.
Analysis, presentation, analysis: selection and evaluation of KAIZEN themes
But before the start of the KAIZEN activity with 21 teams, which ran from December 2016 to October 2017, there was a detailed preparatory phase. The preparation started in November 2016 with an analysis and generation of themes by all departments. If a theme was selected based on the topics of the business plan, the teams studied the current situation and described problems as well as challenges like the discrepancy between target and present performance.
The kick-off presentation on December 12, 2016 marked the formal start of the KAIZEN activity. On that day, the members of the SEKISUI S-Lec Board Meeting (SBM) presented the proposed themes of their departments and discussed whether they were appropriate for the KAIZEN activity or not. The SBM consists of 8 members in total and represents the highest management level at SEKISUI S-Lec. The only decisive factor was whether the project is able to improve everyday work in the future or not.
The teams whose themes were selected in this way then started with detailed analyses of concrete situations at the beginning of 2017. For example, SEKISUI S-Lec has a packaging department. In this phase, the team of the support project “Repacking big bags” analysed the causes of the lifting and packing of larger items, which is why the workers regularly had strains on their bodies. The team wondered how it would be easier for workers to carry out this task in the future, in order to protect their health and meet the needs of older colleagues.
Coaching: nine steps to success
After the detailed analysis was completed, the actual KAIZEN activity started. The course of the activity is closely linked to the nine steps of KAIZEN, which is considered a guideline for the work of the teams. To ensure that the teams pass through all nine KAIZEN phases, Hikono san, KAIZEN Manager at SEKISUI Europe and responsible for the KAIZEN activities in Europe, developed a corresponding format.
In order to make it easier for the teams to adhere to the format and thus ensure a smooth process, there were four coaching sessions with Hikono san during the ongoing KAIZEN activity at SEKISUI S-Lec in February, April, June and September. For these dates, Hikono san travelled to SEKISUI S-Lec for two days each and coached the teams individually based on the current status of their projects.
“Judgement Days”: internal KAIZEN competition days and the award ceremony
The two winners of the internal KAIZEN activity – there was one winner per plant – were determined during the internal competition days on 12 and 13 October. Each of the two plants hosted a competition day. The jury that decided on the winners is made up of five of the eight SBM members.
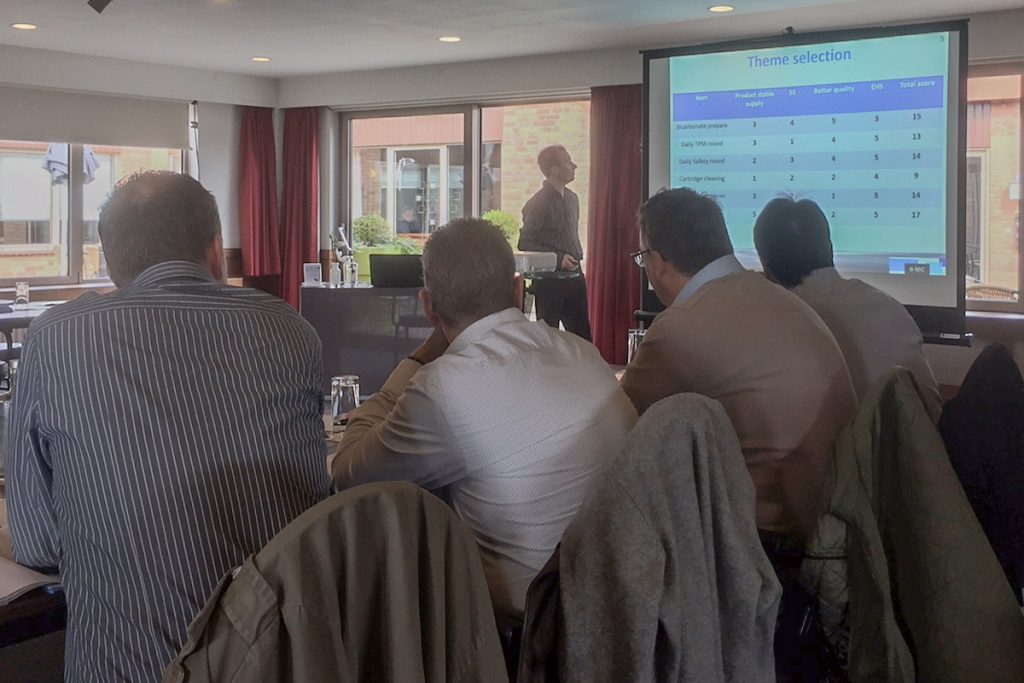
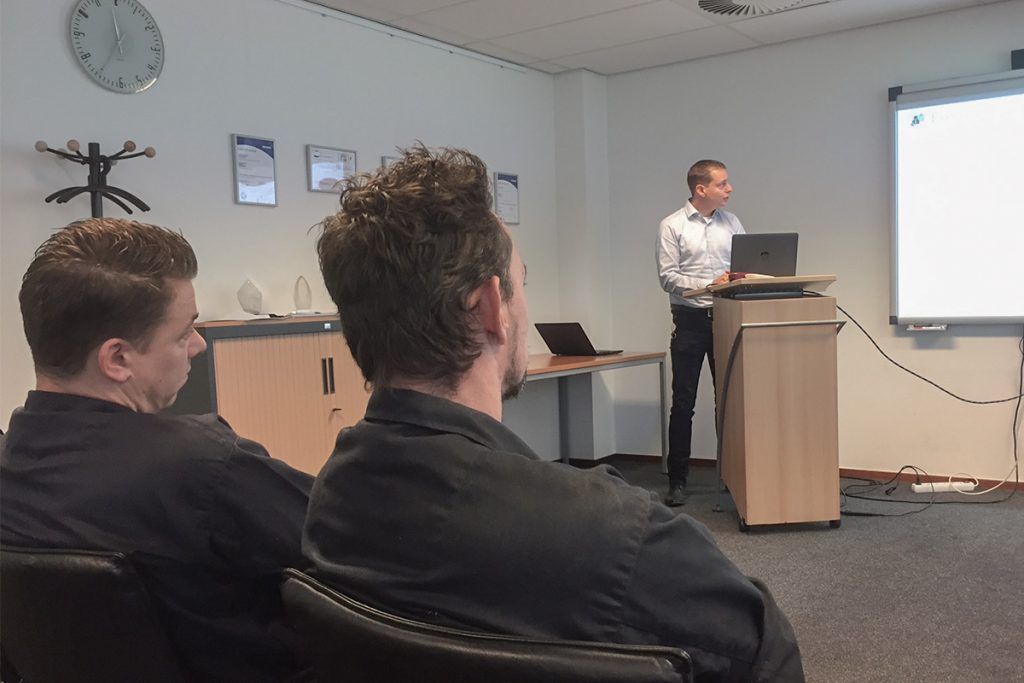
During these two days the 21 teams presented their projects. Each team had total of 20 minutes to introduce their work and convince the jury of their undertaking in a subsequent Q&A round. The two winners were announced on 16 October during the internal award ceremony and will travel to Düsseldorf on 21 November to take part in the seventh KAIZEN Conference.