KAIZEN is integral to SEKISUI culture, a defining philosophy that inspires us to constantly evaluate, refine and progress. Almost every employee has heard of the term “KAIZEN”, but may be unsure about the meaning. In this article, we want to explain the process, so everyone can integrate the Japanese philosophy into daily work life.
Every SEKISUI employee has heard the word “KAIZEN”. But what does it actually mean?
To start with a basic definition: The Japanese word “KAIZEN” means “change for better”.
In our businesses, KAIZEN refers to activities that continuously improve all functions and involve all employees from President to factory workers. At SEKISUI, mastering KAIZEN is an action plan for success.
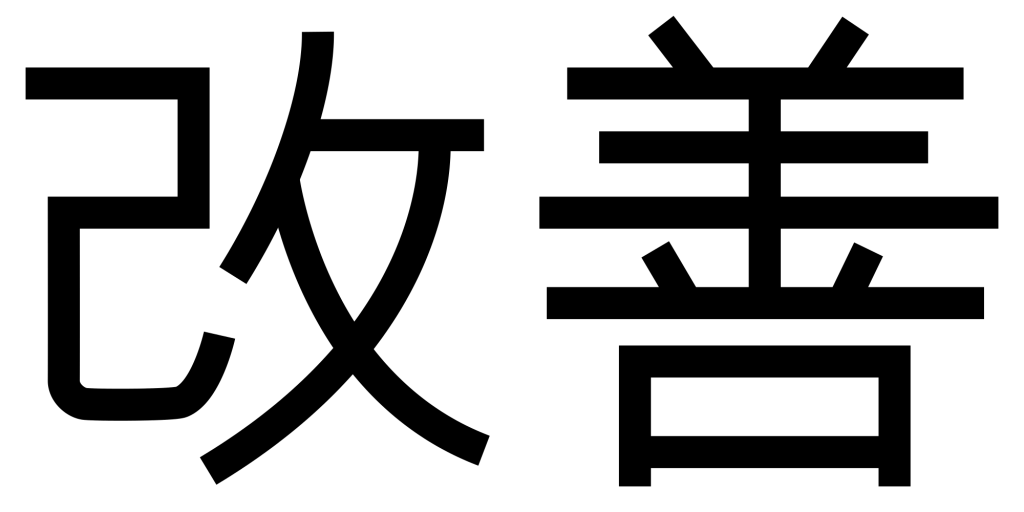
KAIZEN activities are done for improvements in quality and productivity and increasing efficiency
The ultimate purpose of KAIZEN is human development. Because acting like KAIZEN thinking will have positive consequences on your life (not only at work). The question “How can I make this process easier?” is the ultimate KAIZEN methodology to overcome obstacles in everyday life, in a disciplined way.
Going ahead, KAIZEN is a nine-step process of continuous improvement that is of high priority for all SEKISUI businesses. The steps range from identifying the problem to taking action, confirming results and planning ahead, so a problem won’t recur:
- Step 1 Theme selection
- Step 2 Current situation investigation
- Step 3 Target setting
- Step 4 Action plan
- Step 5 Cause analysis
- Step 6 Countermeasure processing/ Implementation
- Step 7 Effect confirmation
- Step 8 Standardization
- Step 9 Future plan
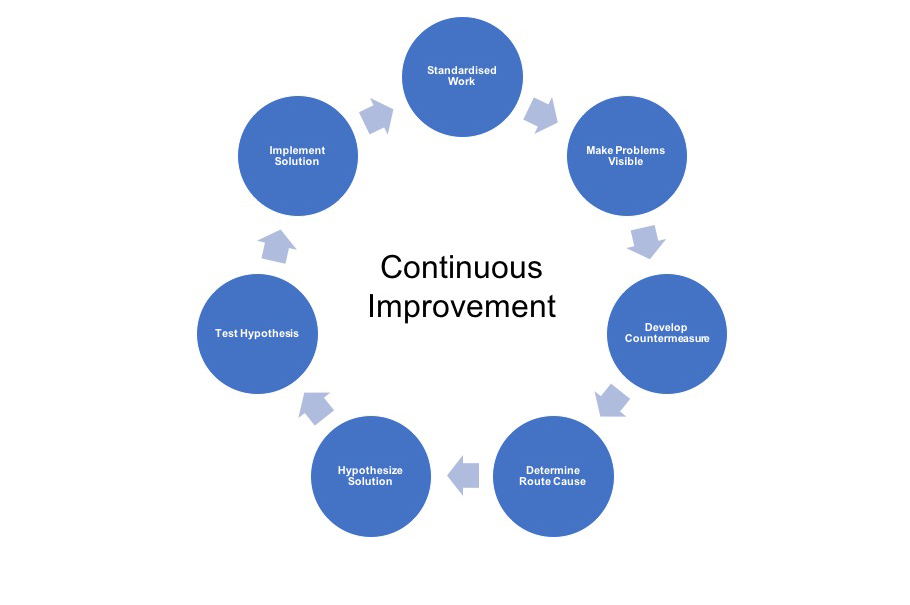
KAIZEN activities at SEKISUI
SEKISUI has introduced hands-on KAIZEN activities in 1966 as quality control (QC) groups which later evolved into small group activities. Staff from each site form small groups, choose a problem in order to improve quality and productivity, solve it using the KAIZEN method and present their results as part of an annual competition – to share information and help each other improve.
Read here about the last European convention: https://newsroom.sekisui.eu/the-7th-european-KAIZEN-convention/
Questions you might have about KAIZEN – and all the answers
Which processes can be matter of a KAIZEN activitiy?
Is KAIZEN part of my everyday workload?
The KAIZEN group projects, which are part of the yearly convention, are voluntary and considered additional to regular work. Have a look at some of the teams and their projects here: https://newsroom.sekisui.eu/the-teams-of-the-sekisui-KAIZEN-convention-2017/
How can I participate in a KAIZEN team?
- SEKISUI Alveo: Henk Dohmen (henk.dohmen@SekisuiAlveo.com)
- SEKISUI Diagnostics: Darren Ladd (darren.ladd@sekisuidiagnostics.com)
- SEKISUI Eslon: Marco Waanders (mwaanders@eslon.nl)
- SEKISUI S-Lec: Rene Venner (rene.venner@s-lec.nl)
- SEKISUI Specialty Chemicals: Margarita Negrete (margarita.negrete@sekisui-sc.com)